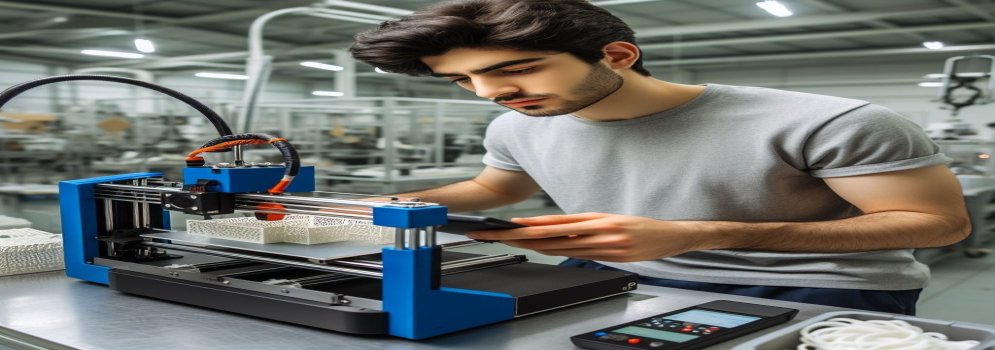
چاپ سه بعدی، همچنین به عنوان ساخت افزایشی شناخته می شود، فرآیندی است که در آن از یک فایل دیجیتال برای ایجاد یک شیء جامد سه بعدی استفاده می شود. در فرآیند چاپ سه بعدی، لایه های متوالی مواد توسط "چاپگر سه بعدی" تا زمان تکمیل ساخت شیء گذاشته می شود.
اشیاء چاپ شده سه بعدی از طریق یک فرآیند افزایشی ایجاد می شوند، جایی که چاپگر لایه به لایه مواد را روی هم قرار می دهد تا شکل مورد نظر "چاپ" شود. هر لایه را می توان به عنوان یک برش عرضی نازک از شیء چاپ شده در نظر گرفت. با چاپ سه بعدی، کاربران می توانند اشکال پیچیده ای را بدون نیاز به مصرف مواد به اندازه روش های تولید سنتی تولید کنند.
سبک عملکرد چاپ سه بعدی برعکس "ساخت و ساز کاهشی" است، جایی که مواد با استفاده از تجهیزاتی مانند دستگاه فرز بریده یا خالی می شوند. برعکس، ساخت افزایشی برای ایجاد اشیاء فیزیکی به قالب یا بلوک ماده نیاز ندارد. در عوض، لایه هایی از مواد را روی هم چیده و آنها را به هم جوش می دهد.
چاپ سه بعدی امکان ایجاد سریع محصول، هزینه های پایین برای زیرساخت ثابت اولیه و توانایی ایجاد هندسه های پیچیده با استفاده از انواع مواد مختلف را فراهم می کند، چیزی که راه حل های تولید سنتی ممکن است به طور کارآمد انجام ندهند.
تاریخچه چاپ سه بعدی
چاپ سه بعدی که به طور کلی با فرهنگ "خودت انجام بده" (DIY) آماتورها و علاقه مندان مرتبط است، به کاربردهای تجاری و صنعتی نیز گسترش یافته است. به عنوان مثال، مهندسان امروزه اغلب از چاپگرهای سه بعدی برای نمونه سازی و ایجاد اشیاء هندسی سبک وزن استفاده می کنند.
ریشه های چاپ سه بعدی در "نمونه سازی سریع" نهفته است. هنگامی که فناوری پایه برای اولین بار در دهه 1980 اختراع شد، از این اصطلاح برای توصیف آن استفاده می شد، زیرا در آن زمان، چاپ سه بعدی فقط برای ایجاد نمونه اولیه به جای قطعات تولیدی مناسب بود. در واقع، هدف اصلی از ایجاد آن به سادگی سرعت بخشیدن به توسعه محصولات جدید از طریق نمونه سازی سریع بود.
جالب اینجاست که این فناوری در زمان معرفی اولیه توجه زیادی را به خود جلب نکرد. در سال 1981، هیدئو کوداما از ژاپن اولین حق اختراع را برای ماشینی ثبت کرد که از نور UV برای سفت کردن فتوپلیمرها استفاده می کرد. سه سال بعد، مخترعان فرانسوی الیویه د ویت، ژان کلود آندره و آلن ل مهایت به طور مشترک برای فناوری مشابهی ثبت اختراع کردند. هر دو حق ثبت اختراع رها شدند و جنرال الکتریک اعلام کرد که "مورد دوم فاقد پتانسیل تجاری قابل توجهی است".
در سال 1984 بود که چارلز هال، مخترع آمریکایی، حق اختراعی را برای "دستگاهی برای تولید اشیاء سه بعدی توسط استریولیتوگرافی" ثبت کرد. او فایل STL را اختراع کرد و سه سال بعد، در سال 1987، شرکت 3D Systems را تأسیس کرد.
در همان دهه، با ثبت اختراع برای ت frit sintering لیزری (SLS) و مدل سازی رسوب ذوب شده (FDM)، گام های مهمی در فضای چاپ سه بعدی ایالات متحده برداشته شد. Desktop Manufacturing (DTM) Corp. و Stratasys شرکت های پیشگام در زمینه چاپ سه بعدی بودند که تقریباً در همان زمان تأسیس شدند.
پس از آن، با تجاری سازی سریع صنعت، این صنعت متحول شد. اولین «چاپگرهای سه بعدی» بزرگ و پرهزینه بودند و سازندگانشان برای به دست آوردن قراردادهای نمونه سازی صنعتی با تولیدکنندگان بزرگ خودرو، کالاهای مصرفی، محصولات بهداشتی و هوافضا رقابت می کردند.
تا سال 1987، شرکت 3D Systems اولین چاپگر SLA با کیفیت تجاری را معرفی کرده بود. در سال 1992، Stratasys و DTM اولین چاپگرهای تجاری FDM و SLS را به ترتیب عرضه کردند. اولین چاپگر سه بعدی فلزی در سال 1994 توسط Electro Optical Systems (EOS)، یک شرکت آلمانی معرفی شد.
با آغاز هزاره جدید، شرکتهای فعال در فضای چاپ سه بعدی برای کسب سود به شدت رقابت میکردند. پیشرفت در علم مواد و انقضای بسیاری از اختراعات، مقرون به صرفه بودن چاپ سه بعدی را افزایش داد.
به زودی، به لطف پیشرفت هایی که در زمینه چاپ سه بعدی صورت گرفت، فرآیندهای تولید دیگر به طور انحصاری در اختیار شرکت های بزرگ با ماشین آلات سنگین و سرمایه کلان نبود. امروزه، چاپ سه بعدی به یک راه حل پیشرفته برای ساخت انواع مختلف قطعات تولیدی تبدیل شده است.
چگونه چاپ سه بعدی کار می کند؟
استاندارد ایزو/آستام ۵۲۹۰۰ که به اصول و اصطلاحات کلی در ساخت افزایشی مربوط می شود، فرآیندهای چاپ سه بعدی را به هفت گروه مجزا دسته بندی می کند. هر نوع چاپ سه بعدی کمی متفاوت عمل می کند.
مدت زمان چاپ یک شیء سه بعدی به نوع چاپ، اندازه خروجی، نوع ماده، کیفیت مورد نظر و پیکربندی تنظیمات بستگی دارد. چاپ سه بعدی می تواند از چند دقیقه تا چند روز طول بکشد.
انواع مختلف چاپ سه بعدی عبارتند از:
- ذوب بستر پودری (Powder Bed Fusion - PBF)
در ذوب بستر پودری، انرژی حرارتی به شکل پرتو الکترونی یا لیزر، به طور انتخابی مناطق خاصی از یک بستر پودر را برای ایجاد لایه ها ذوب می کند. این لایه ها روی هم ساخته می شوند تا یک قطعه ساخته شود.
ذوب بستر پودری ممکن است شامل فرآیندهای تف جوشی یا ذوب باشد، با این حال روش اصلی عملکرد همچنان یکسان باقی می ماند. ابتدا، یک غلتک یا تیغه پوشش دهنده، لایه نازکی از پودر را روی سکوی ساخت قرار می دهد. سپس، سطح بستر پودر با استفاده از یک منبع حرارتی اسکن می شود. این منبع به طور انتخابی دمای ذرات را برای اتصال مناطق خاص افزایش می دهد.
هنگامی که منبع حرارتی یک مقطع عرضی یا لایه را اسکن می کند، سکوی ساخت پایین می آید تا فرآیند برای لایه بعدی تکرار شود. خروجی نهایی یک حجم با قسمت های ذوب شده است، در حالی که پودر اطراف بدون تأثیر باقی می ماند. سپس سکوی ساخت بالا می رود تا امکان بازیابی قطعه ساخته شده را فراهم کند. ذوب بستر پودری شامل چندین روش چاپ استاندارد مانند ت frit لیزری انتخابی (SLS) و ذوب مستقیم لیزری فلز (DMLS) می شود.
از SLS به طور مرتب برای ساخت قطعات پلیمری برای نمونه سازی و قطعات کاربردی استفاده می شود. چاپ SLS با بستر پودر به عنوان تنها سازه نگهدارنده انجام می شود. عدم وجود سازه های نگهدارنده اضافی امکان ایجاد هندسه های پیچیده را فراهم می کند. با این حال، قطعات تولید شده اغلب دارای تخلخل داخلی و سطح دانه دار هستند و به طور کلی نیاز به پس پردازش دارند.
SLS شبیه به ذوب لیزری انتخابی (SLM)، ذوب بستر پودری با پرتو الکترونی (EBPBF) و ذوب مستقیم لیزری فلز (DMLS) است. با این حال، از این فرآیندها برای ایجاد قطعات فلزی استفاده می شود و برای ذوب ذرات پودر به صورت تک لایه به لیزر تکیه می کنند.
DMLS دمای ذرات را فقط تا نقطه ذوب افزایش می دهد، جایی که آنها در سطح مولکولی ترکیب می شوند. از سوی دیگر، SLM ذرات فلز را به طور کامل ذوب می کند. هر دوی این تکنیک ها نیازمند حرارت زیاد هستند و بنابراین به سازه های نگهدارنده نیاز دارند. پس از پایان فرآیند، سازه های نگهدارنده با استفاده از ماشین کاری CNC یا به صورت دستی برداشته می شوند. سپس قطعات برای رفع تنش های باقیمانده در طی پس پردازش تحت عملیات حرارتی قرار می گیرند.
این تکنیک های چاپ سه بعدی فلز قطعاتی با خواص فیزیکی با کیفیت بالا ایجاد می کنند، که گاهی حتی از فلز پایه مورد استفاده نیز قوی تر هستند. همچنین، کیفیت سطح نهایی آنها اغلب عالی است. از نظر مواد، این تکنیک ها می توانند سوپر آلیاژهای فلزی و سرامیک هایی را پردازش کنند که استفاده از آنها در فرآیندهای دیگر دشوار باشد. با این حال، هر دو DMLS و SLM پرهزینه هستند و حجم سیستم اندازه خروجی را محدود می کند.
- فت پلیمریزاسیون با وان (VAT Photopolymerization)
فت پلیمریزاسیون با وان را می توان به دو روش تقسیم کرد: پردازش نور دیجیتال (DLP) و استریولیتوگرافی (SLA). هر دو این فرآیندها با استفاده از منبع نور برای سفت کردن انتخابی مواد مایع (معمولا رزین) ذخیره شده در یک وان، به صورت تک لایه قطعه ایجاد می کنند.
DLP با "فلش زدن" تصویر تکمیل شده هر لایه روی سطح مایع درون محفظه کار می کند. از طرف دیگر، SLA برای سفت کردن مایع از یک منبع نور ماوراء بنفش تک نقطه ای یا لیزر استفاده می کند. پس از اتمام چاپ، رزین اضافی باید از خروجی تمیز شود و سپس قطعه باید در معرض نور قرار گیرد تا استحکام آن بیشتر شود. سازه های نگهدارنده، در صورت وجود، باید بعد از چاپ (پس پردازش) حذف شوند و همچنین می توان برای دستیابی به کیفیت سطح بالاتر، قطعه را بیشتر پردازش کرد.
این روش ها برای خروجی هایی که نیاز به دقت ابعادی بالایی دارند بسیار مناسب هستند، زیرا می توانند قطعاتی با جزئیات دقیق و با کیفیت عالی ایجاد کنند. بنابراین DLP و SLA برای تولید نمونه های اولیه بسیار مناسب هستند.
با این حال، خروجی این روش ها اغلب شکننده است و آنها را برای نمونه های اولیه کاربردی (قطعاتی که قرار است کارایی داشته باشند) کم تر مناسب می کند. رنگ و خواص مکانیکی این قطعات نیز به احتمال زیاد در اثر نور ماوراء بنفش خورشید خراب می شود و آنها را برای استفاده در فضای باز نامناسب می کند. در نهایت، اغلب به سازه های نگهدارنده نیاز است که ممکن است جای لکه هایی را باقی بگذارند، که می توان آنها را از طریق پس پردازش حذف کرد.
- اتصال جت (Binder jetting)
اتصال جت با قرار دادن یک لایه نازک از مواد پودری، مانند ماسه پلیمری، سرامیک یا فلز، روی سکوی ساخت کار می کند. پس از این، یک هد چاپ قطرات چسب را برای اتصال این ذرات رسوب می دهد. بدین ترتیب قطعه به صورت لایه به لایه ساخته می شود.
قطعات فلزی باید به صورت حرارتی تند ذوب (sintered) شوند یا با فلزی با نقطه ذوب پایین مانند برنز نفوذپذیر (infiltrated) شوند. قطعات ساخته شده از سرامیک یا پلیمر تمام رنگی را می توان با استفاده از چسب سیانو اکریلات اشباع کرد. به طور کلی برای تکمیل خروجی، پس پردازش مورد نیاز است.
اتصال جت کاربردهای زیادی از جمله قالب های سرامیکی در ابعاد بزرگ، نمونه های اولیه تمام رنگی و چاپ سه بعدی فلز دارد.
- جت مواد (Material jetting)
جت مواد از لحاظ مفهومی شبیه به چاپ جوهری است. با این حال، به جای قرار دادن جوهر روی کاغذ، از یک یا چند هد چاپ برای ایجاد لایه هایی از مواد مایع استفاده می کند. هر لایه قبل از ایجاد لایه بعدی خشک (cure) می شود. در حالی که جت مواد به سازه های نگهدارنده متکی است، این سازه ها را می توان با استفاده از ماده ای قابل حل در آب ساخت که پس از تکمیل ساخت قابل شستشو است.
این فرآیند بسیار دقیق برای ایجاد قطعات تمام رنگی با استفاده از انواع مختلف مواد مناسب است. با این حال، این روش پرهزینه است و خروجی آن تمایل به شکنندگی و تجزیه شدن دارد.
- مدل سازی رسوب مذاب (Fused deposition modeling - FDM)
در مدل سازی رسوب مذاب (FDM)، از یک نازل گرم شده برای تغذیه قرقره فیلامنت به هد اکستروژن استفاده می شود. هد اکستروژن دماي مواد را بالا می برد تا نرم شود و قبل از قرار دادن آن در نواحی از پیش تعیین شده برای خنک شدن، آن را نرم کند. پس از ایجاد یک لایه ماده، سکوی ساخت پایین می آید و برای قرار دادن لایه بعدی آماده می شود.
این فرآیند که با نام اکستروژن مواد نیز شناخته می شود، دارای زمان آماده سازی کوتاه و مقرون به صرفه است. با این حال، دقت ابعادی آن کم است و برای داشتن یک سطح صاف اغلب به پس پردازش نیاز دارد. خروجی این روش همچنین برای کاربردهای حساس مناسب نیست زیرا تمایل به ناهمسانگردی (anisotropic) دارد، یعنی در یک جهت ضعیف تر است.
- لمینیت ورق (Sheet lamination)
لمینیت ورق را می توان به دو فناوری دیگر طبقه بندی کرد: ساخت افزودنی فراصوت (UAM) و ساخت اشیاء لمینت (LOM). UAM نیاز به انرژی و دمای کمی دارد و با اتصال ورق های نازک فلزی با استفاده از جوشکاری فراصوت کار می کند. این روش با چندین فلز از جمله فولاد ضد زنگ، تیتانیوم و آلومینیوم کار می کند. از سوی دیگر، LOM به طور متناوب لایه هایی از مواد و چسب را برای ایجاد خروجی نهایی قرار می دهد.
- رسوب انرژی مستقیم (Direct energy deposition)
این تکنیک از لیزر، قوس الکتریکی، پرتو الکترونی یا نوع دیگری از انرژی حرارتی متمرکز برای ذوب کردن پودر یا مفتول (wire feedstock) در حین قرارگیری استفاده می کند. این فرآیند به صورت افقی برای ایجاد لایه ها انجام می شود که سپس به صورت عمودی برای ساخت قطعه روی هم چیده می شوند. این روش برای انواع مختلف مواد از جمله سرامیک، پلیمر و فلز مناسب است.
منبع : cafeelec.ir